A crane brake upgrade provides crane owners/operators a way to keep their equipment working safely, reliably, and without the typical headaches caused by old and obsolete crane brakes.
Often, decades old cranes are still operational, but the original brakes have become obsolete with spare parts needed for repair either no longer available or prohibitively expensive. In such cases, we support our customers with a crane brake upgrade by retrofitting a modern industrial brake in place of the old brake. By upgrading their old crane brakes, customers are able to meet the latest industry standards and improve the performance and reliability of their crane. Additionally, with the new crane brakes installed, we can provide the customer with technical support, service, spare parts, and repairs for decades to come.
Below, we outline key considerations when upgrading and replacing old crane brakes:
Crane Brake Location & Function
To specify the appropriate replacement brake system, it is important to determine the location and function of the existing crane brake. For example, the brake may be located on the bridge drive, trolley drive, main hoist, auxiliary hoist, or potentially the gantry drive.
Documentation of whether the brake is used for stopping or just holding the load is also essential. If the motor driving the load is connected to a variable frequency drive, the brake may only be needed for holding the load, since the drive can be used to stop the load before the brake is set.
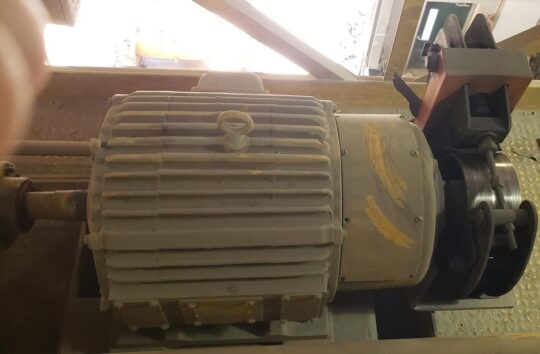
This bridge crane travel drive brake is an ideal candidate for replacement due to its age and the poor availability of parts and support.
Torque Requirement
With this information on existing crane brake location and function established, a suitable replacement brake can be selected. The replacement brake should have at least as much, if not more, torque capacity as the original brake.
In most instances, we can determine the necessary torque capacity by referencing the previous brake nameplate if it is available. If the original torque capacity is unknown and information on the original brake is not available, the brake must instead be selected by determining the full load motor torque at the brake shaft location. This is accomplished by calculating the full load motor torque using the rated motor horsepower and RPM.
If the brake is used for bridge, trolley, or gantry operation, a 1.7 safety factor is applied over the calculated nominal full load motor torque. If the brake is on the hoist, a minimal 2.0 safety factor is used.
Method of Brake Release
Since the brakes on cranes are failsafe, the means of releasing the brake must be determined. For DC-powered cranes, electromagnetic released drum brakes are commonly used, while for cranes with 460V, 60 Hz, three-phase power, electrohydraulic thruster-released drum brakes are a cost-effective alternative.
Installation Considerations
Once the replacement crane brake is selected, we help the customer analyze the installation space to determine if the new brake will require changes to the mounting structure.
Some brakes conform to standardized configurations – in those cases, the new brake can be bolted into the place of the old brake and we can re-use the existing brake drum and brake mounting configuration. This is typically our preference, as it makes for easy installation of the new brake and is cost effective due to re-using the brake drum.
However, some of the much older braking systems may require modification to the mounting structure in order to accept a modern brake. In some cases involving very outdated braking systems using non-standard brake sizes, a smaller new brake style can be used due to the higher torque capacities of newer brakes. Using a smaller brake drum can help gain some vertical clearance between the brake base and the horizontal centerline, which helps with ease of installation.
Crane Brake Features & Options
Lastly, when upgrading old crane brakes, we consider various brake features/options. These optional features are relatively new technologies and would not have been available when these old cranes were originally built, but selecting the appropriate set of optional features for the new brake will help provide maintenance-free operation and improved performance.
These optional features should be selected based largely on the application including the location and function of the brake. Examples of these optional features include: automatic wear adjustment (ideal for stopping applications subject to high pad wear rates), limit switches for indication “brake released” and “lining wear” (ideal for making sure the brake is releasing prior to motor operation and avoiding damage to the brake drum if the lining wears out), manual hand release lever (ideal for slipping the load during maintenance or a power failure situation), and thrusters equipped with lowering valves (ideal for bridge travel operation requiring gentle braking action).
The operating environment of the brake should also be considered as it relates to other system features/options. For example, our brakes can be specified for high or low ambient temperatures, with extra protection from corrosive dust, and/or with various enclosure or cover designs if the brake is exposed to the elements.
By performing a crane brake upgrade, customers can improve the reliability, efficiency, and safety of their aging cranes. Our team of experts is available to help with the selection and installation of suitable brake systems.