Crane emergency hoist brakes are an important safety feature for any operation making critical lifts. Thankfully, these industrial braking systems which are most commonly seen in steel mill applications are increasingly being adopted by operators across industries who take a proactive approach to safety.
Emergency hoist brakes prevent accidents by stopping a load from falling in the event of a failure of a crane hoist mechanism. Root causes of the hoist failure range from a broken input shaft, to a input shaft brake failure (often due to either improper adjustment or not having automatic lining wear compensation), to a various types of gearbox and low-speed shaft failures. In any situation where you depend only on a motor brake, you are exposed to failures where the connection between the motor and hoist rope drum is severed. Such catastrophic failures can create a hazardous situation leading to equipment damage or, worse, loss of life. The solution to this dangerous situation lies in installing an emergency safety brake on the output side of the system, either on the gearbox output shaft or the hoist rope drum flange.
Below, our industrial brake experts weigh in on various aspects of emergency brakes used on crane hoists in a variety of industries and applications.
How Emergency Brakes Work – Location & Function
Emergency brakes are typically redundant systems featuring spring-applied failsafe mechanisms that remain in a released position while the hoist is operational. Unlike service brakes on the input shaft, they do not cycle on and off with each lift. In the event of an e-stop, hoist overspeed fault, or loss of power, the emergency brakes set immediately on the output (or low-speed) side of the system.
How to Specify an Emergency Hoist Brake
To specify an emergency braking system for the output of a geared system, we need to determine the nominal full load torque at the shaft where the emergency brake will be located. The process starts with determining the rated horsepower and RPM of the motor at the input shaft, from which we can calculate the full load torque of the motor. We then multiply this torque by the gearbox’s gear ratio to determine the nominal gearbox output torque, which is then multiplied by a safety factor of 1.5. The emergency brake torque rating must exceed this final value.
In other cases the stopping time of the load is a main consideration. In this instance we have to find the line pull at the rope drum, the total mass moment of inertia at the rope drum, and the rope drum RPM. With this information, we can determine how far the load will drop when the brakes set.
Commonly Used Emergency Hoist Brakes & Features
In many instances, the output shaft’s torque rating can be quite high, making it unsuitable for drum brakes and smaller thruster-released disc brakes. In such cases, larger spring-applied, hydraulically released disc brake calipers, such as single piston, floating calipers, or dual piston fixed calipers are more appropriate.
Emergency brakes undergo very little lining wear since the disc stops rotating by the time the brakes engage in normal operation. Nevertheless, we always install limit switches on the brakes to indicate “brake released” and “lining wear adjust needed.” This approach alerts the operator to adjust the brake if there are any conditions that have caused lining wear. Similarly, the “brake released” switch signals that the hydraulic system is functioning correctly, the brake has released, and the hoist motor can be started.
When using hydraulically released brakes, the braking system typically uses its own dedicated hydraulic release power unit. Our standard compact units are available for brake cycle rates of less than 50 per hour, while our high capacity hydraulic release power units are specified for brake cycle rates of greater than 50 per hour. All of our HPUs are also equipped with manual hand release pumps in case of power loss. Optional HPU features include high temperature and low fluid level monitoring.
Other Types of Emergency Hoist Brakes
In some applications, there are ambient conditions which make the use of pneumatic or electromagnetic failsafe brakes preferable over hydraulic brakes. This happens in plant environments where the presence of hydraulic fluid is undesirable.
When designing a system using pneumatic failsafe brakes, we will often use multiple calipers to satisfy the torque requirement. When using electromagnetic failsafe brakes, we can achieve high torque values and often meeting the torque requirement with a single caliper, although the drawback of this approach is the inherent high-cost of large electromagnetic braking systems which also require the use of a brake rectifier/controller.
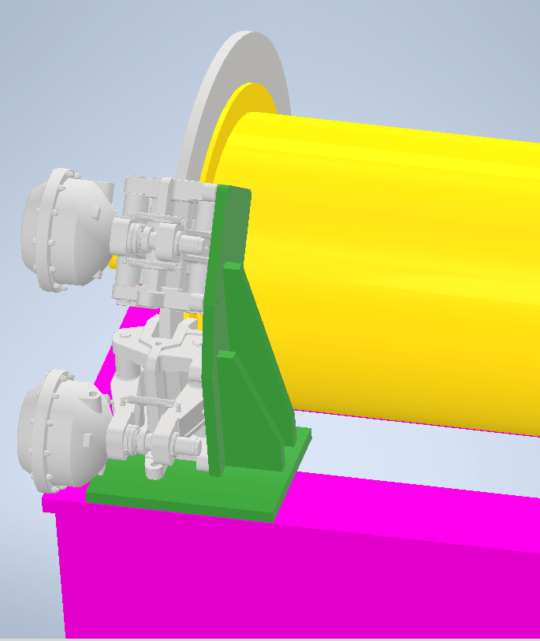
Solutions involving multiple pneumatic brake calipers acting on a hoist rope drum are a viable alternative to higher torque hydraulic systems. Pneumatic systems such as this one often require a custom mounting stand to accommodate multiple brake calipers.
Emergency Hoist Brake Retrofit Applications & Considerations
While it is ideal to incorporate emergency hoist brakes into the original crane design, the vast majority of older cranes were never equipped with emergency safety brakes. In these cases, Hindon advises the customer on the proper technical data needed to retrofit the brakes to the older crane. Typically, this requires modification to the rope drum with the addition of a brake disc, as well as developing a custom brake mounting console to tie into the existing crane structure. We use 3D solid models and FEA to inform these design efforts and to help ensure the mounting console is sufficiently rigid to support the braking load.
Maintenance Considerations
It’s worth emphasizing that emergency brakes are essential whenever a load is being lifted over people or if there’s a possibility of significant equipment damage in the event that there is a driveline failure and the load is lost. Whether designing new equipment or upgrading older equipment with a retrofit project, a properly designed and maintained emergency hoist braking system can help avoid this type of costly and catastrophic accident. Keeping a failsafe spring applied brake in proper adjustment is absolutely essential, because as the linings wear, the springs are decompressed and the available braking forces are reduced. This is why monitoring pad wear is so important, even though pad wear in normal operation is often negligible.
Our team of experts is experienced in supporting customers across a variety of industries with such systems and are available to help with the selection and installation of these critical industrial braking systems.