Background:
In support of the end user, an integrated steel producer and merchant of steel products, an engineering firm contacted Hindon for assistance with an emergency braking system for use on a conveyor at a Midwest steel mill. The conveyor transports material for mill operations and includes downhill sections, requiring a fail-safe emergency brake to secure the loaded conveyor in the event of power loss.
The end user required a high-torque fail-safe disc braking system suitable for a demanding steel mill environment prone to significant accumulation of dust and dirt. Additionally, the project was constrained by spatial limitations due to a removable floor plate adjacent to the gearbox output shaft where the braking system was to be installed.
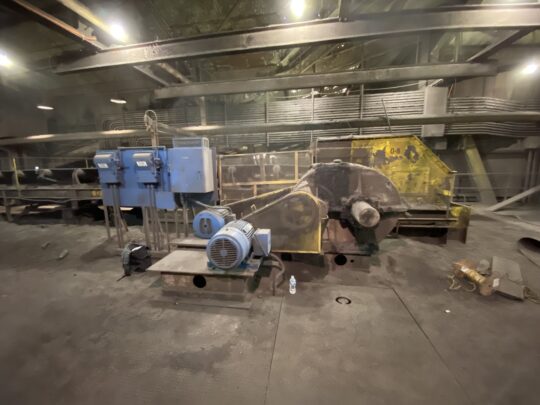
Layout of conveyor drive system in need of an emergency brake.
Application Challenges:
- High braking torque requirement with spatial limitations
- Demanding operating conditions associated with a corrosive steel mill environment
Solution:
Working with the engineering firm in support of the end user, Hindon developed a robust and reliable emergency braking system for the conveyor.
Hindon designed and supplied a spring-applied electrohydraulic thruster-released braking system for use on a custom disc/hub assembly. All components of the thruster disc brake were prepared specifically for use in a steel mill environment including sintered linings, proximity limit switches to indicate “brake released” and “lining wear,” automatic lining wear compensation, a manual release lever, and an adjustable time delay in the electrohydraulic thruster to ensure smooth braking action and minimal wear on conveyor components.
Hindon’s custom brake disc/hub assembly became a critical component in this system, maximizing disc diameter and braking torque without requiring any modifications to the the existing system or interfering with the removable floor plate near the gearbox shaft.
This robust braking system was easily installed and commissioned, operates reliably as intended, and returned a more than satisfactory result for the end user.