Background:
Working in support of the end user, a U.S. building material manufacturer, Hindon’s customer, an engineering firm that specializes in capital improvement projects for industrial clients, needed to add additional industrial brakes to a fiber insulation press packing system. The existing servo brake motors on the fiber packaging machine proved inadequate when subjected to back pressure from compressing fiber insulation-filled bags into packages, resulting in creeping.
As a solution, the customer endeavored to add external brakes to the press packing system – both on the pusher chain drive and on the compression tunnel chain drive. The brakes had to be mounted on the driven shafts and would serve as holding brakes when the pusher or compression tunnel press plate reached its destination with the servo motors powered off. Upon completion of the corresponding process, the brakes would be powered back on and the pusher or compression tunnel press plate would retract to its original position.
Given Hindon’s experience providing application-specific industrial braking solutions across industries, as well as Hindon’s experience with retrofit applications, Hindon was a natural fit to design and supply the ideal braking system for this application.
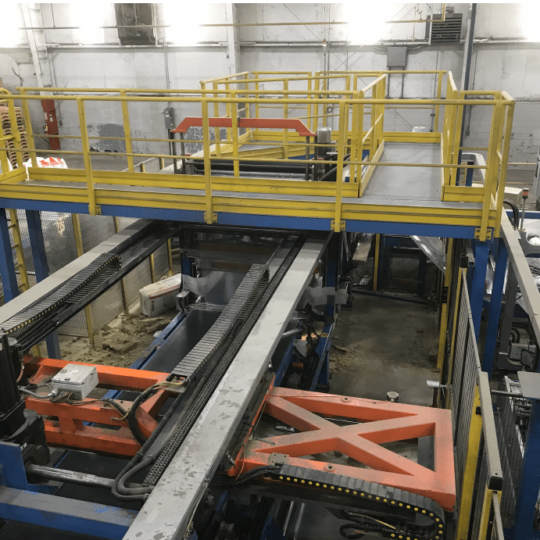
The existing multipack press system was equipped with servo brake motors that proved to be inadequate.
Application Challenges:
- High duty cycle and fast response time requirements
- Retrofit application with existing space constraints
- Compressed project timeline and delivery requirement
Solution:
After evaluating the available technical information on the existing press packing system, as well as discussing project goals, constraints, and other technical requirements with the customer and end user, Hindon designed and supplied an industrial braking system that utilized pneumatically released disc brakes for use on 315mm brake discs with integral hubs. Two brakes were used on the pusher system while one was to be used for the compression tunnel.
Pneumatic fail-safe brakes were ideal for this application for several key reasons. First, the torque requirements (1,740 Nm for the pusher brake and 400 Nm for the compression tunnel) were easily achievable with relatively small pneumatic disc brakes. With the torque requirement satisfied, Hindon needed to ensure the brakes could handle the high duty cycling and fast response times (for brake engagement and disengagement) required by this application – pneumatic brakes were ideal on both fronts. Lastly, pneumatic fail-safe brakes represented a cost-effective and short lead-time solution relative to other alternatives considered including various types of electrically released brakes.
Hindon delivered its industrial braking system within the compressed project schedule, avoiding delays to the overall project completion. Working in partnership with the customer and end user, Hindon successfully provided a robust, reliable, and cost-effective solution that increased the productivity of the packing operation for this U.S. manufacturer.