Background:
A specialized engineering firm focused on serving the pulp and paper industry was contracted by one of the world’s largest privately owned paper, packaging, and distribution companies to provide engineering and design assistance for their paper roll lowerator upender.
The end user’s lowerator upender receives a paper roll of approximately 14,000 lb. in the horizontal position, lowers the roll on a sled, rotates the roll 90 degrees, and places it onto another conveyor in a vertical position.
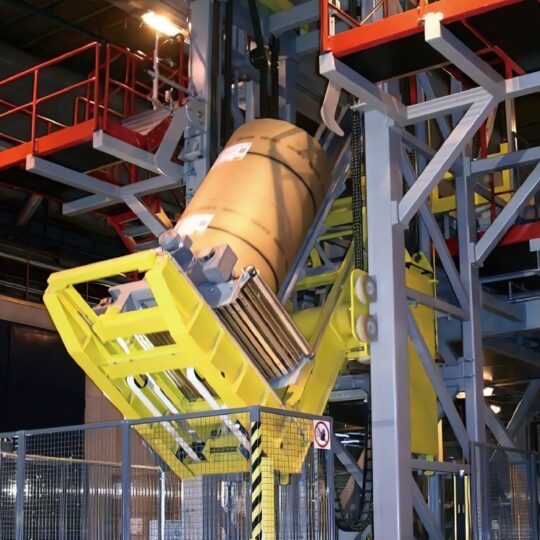
A lowerator upender, a key piece of material handling equipment at a paper factory, in action.
The original emergency braking system installed on the lowerator upender drivetrain was at risk of failing, raising safety and process reliability concerns for the end user in the event of a catastrophic failure or malfunction of the motor brake or gearbox.
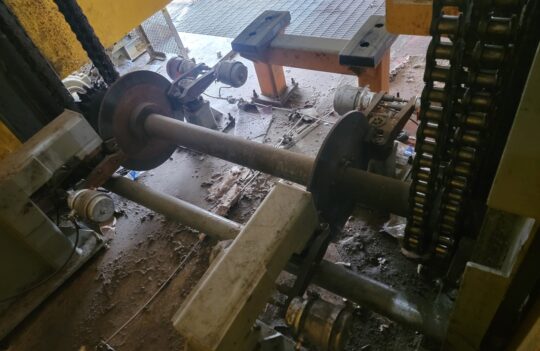
The existing pneumatic caliper disc brake system used for emergency braking on the paper roll upender.
Due in part to Hindon’s experience with designing and supplying retrofit emergency braking systems across various industries, the engineering firm partnered with Hindon to support the end user in identifying the best industrial braking system for this application.
Application Challenges:
- Limited technical information available due to age of existing equipment
- Retrofit application with spatial and mounting constraints
- High torque requirement necessitating the use of a different brake type
Solution:
Through creative collaboration with the customer, Hindon helped the end user and the engineering firm gain a thorough understanding of the original equipment’s design and specifications. This proved to be instrumental in determining the underlying causes of the failure modes experienced by the customer.
Hindon determined that the brakes should remain on the gearbox output shaft to function as true emergency brakes. Also, the existing brake discs and mounting stands would ideally be reused due to the application’s dimensional constraints. After applying an appropriate safety factor using the calculated full load torque, Hindon identified that the existing pneumatic brakes were undersized for the application.
Because the existing brakes were pneumatically released, Hindon investigated several spring applied pneumatically released design options. However, a comprehensive evaluation with other project constraints determined that adequate braking torque could not be provided by pneumatic brakes.
Using these findings, Hindon designed and supplied a hydraulic emergency braking system consisting of four spring applied hydraulically released caliper disc brakes suitable for use on the customer’s two existing 35” diameter discs. This new system also incorporated a compact hydraulic power unit (HPU) for brake control and custom mounting stands engineered for use with the existing brake mounts.
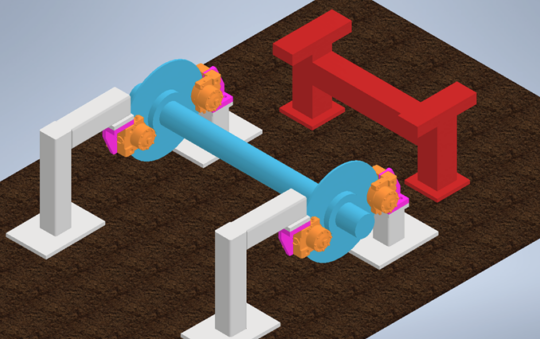
Hindon’s 3D model of the application illustrates the hydraulic caliper braking system (orange) integrated with the existing brake discs (blue) and new custom mounts (magenta) extending from the existing mounts (gray).
This retrofit emergency braking system was ideal for this application for several key reasons.
The use of high torque capacity hydraulic brakes enabled Hindon to design a system with the adequate torque capacity while remaining within the dimensional constraints of the existing braking system. The hydraulically released system also offers a faster reaction time, resulting in reduced pad wear and decreased ongoing maintenance requirements (e.g., brake adjustment).
Hindon’s ability to design and fabricate custom mounting stand adapters that integrate with the existing caliper mounts was critical to providing the most cost-effective solution that aligned with the established dimensional constraints.
With the new emergency braking system’s increased capability, it was essential to evaluate the lowerator upender’s drivetrain and existing caliper mounts to ensure they could withstand the increased torque. This was done using Finite Element Analysis (FEA), wherein the existing system was modeled and subjected to the new higher torque levels. This FEA was used to design the new mounts and ensured the new emergency braking system was compatible with the existing lowerator upender.
This project highlights the potential complexity of designing and supplying a retrofit emergency braking system in a scenario characterized by limited information, multiple potential failure modes, and significant existing project constraints. Working in partnership with the customer in support of the end user, Hindon’s product knowledge, application experience, technical proficiency, and commitment to a thorough evaluation from multiple perspectives yielded a robust, reliable, and cost-effective industrial braking solution for the lowerator upender emergency braking system retrofit.