Background:
A leading U.S. provider of high-quality precast concrete products including parking bumpers, barrier walls, retaining walls, septic tanks, and storm shelters engaged Hindon regarding their urgent need for a replacement overhead bridge crane brake. The customer’s old electromagnetic brake was no longer functioning reliably and the customer was struggling to find parts and support for brake that Hindon was able to identify as obsolete. The customer required a readily available retrofit solution that would get their crane back up and running immediately, while improving the crane’s long-term efficiency and safety.
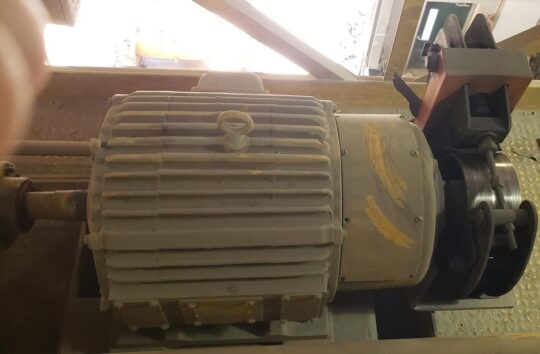
After the customer’s obsolete overhead crane drive brake stopped functioning properly, the customer required a readily available and technically suitable replacement crane brake
Application Challenges:
- Provide a replacement brake with favorable lead-time
- For ease of installation, the ideal brake would be a bolt-in replacement for use on customer’s existing brake drum
- Review of the technical specifications of the drive system and duty of the brake to size the new brake appropriately and specify the ideal brake features
Solution:
After assessing the customer’s existing brake arrangement and reviewing the technical specifications of the crane drive system, Hindon recommended a thruster drum brake as the ideal replacement for the old electromagnetic brake.
Hindon’s thruster drum brake served as a bolt-in replacement for the existing brake and was suitable for use on the customer’s brake drum with no modifications needed. The new brake was equipped with automatic wear adjustment that would ensure consistent and reliable braking, improving the crane’s efficiency and safety while reducing the need for inspections and maintenance. The electrohydraulic thruster used to release the brake was also equipped with an adjustable lowering valve, allowing the customer to set a time delay between when power is removed from the brake and when braking occurs. This couple second delay allows for a smooth braking process, which is ideal for use on bridge travel applications as it helps avoid jarring the crane every time the brakes set.
The installation of the new brake was done without causing any significant downtime to the customer’s operations. By providing a bolt-in replacement brake that was readily available, correctly sized, and included the appropriate features for the application requirements, Hindon’s solution was simple, cost effective, and increased the safety and productivity of the customer’s overhead crane, all while minimizing the customer’s total crane downtime.