Background:
Hindon’s customer is one of the top manufacturers of plant equipment for the ferrous and non-ferrous metal industry. The OEM designs and manufactures specialized equipment such as forges, rolling mills, processing lines, auxiliary equipment, and turnkey plants for steel and metal production and processing throughout the world.
Working in support of a U.S. aluminum mill, the customer needed to upgrade a braking system that had failed on an old aluminum uncoiler unit. The brake on an aluminum mill uncoiler serves a crucial purpose in controlling and managing the speed of the uncoiling process by applying controlled braking force to regulate the tension of the metal coil as it is unwound from the coil reel. By effectively controlling the tension in the metal coil as it is unwound, the brake helps prevent issues such as over-acceleration or excessive tension that can lead to damage or deformation of the aluminum coil, causing issues in downstream processes involving equipment like rolling mills.
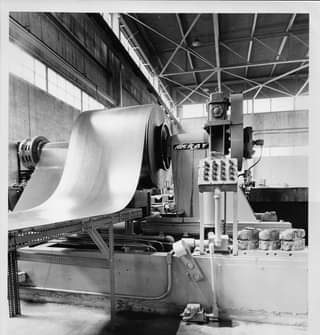
An old aluminum uncoiler with an antiquated pneumatically applied tensioning brake prior to being retrofit with a modernized braking system like one provided by Hindon.
The aluminum mill needed to upgrade their existing low inertia pneumatic brake, which was no longer sufficient for the mill’s needs, to a modern disc brake system that would more reliably support the mill’s increased production levels. Due to the age of the existing uncoiler, reliable technical information for the existing brakes was not readily available.
Leveraging Hindon’s experience in providing application-specific industrial braking solutions and expertise in retrofit applications, collaboration between Hindon and the customer was a natural fit. Working together with the customer, Hindon designed and supplied a replacement hydraulically applied tensioning brake that was easy to install and will support the end user’s increased production levels for years to come.
Application Challenges:
- Limited technical information available due to age of existing equipment
- Conversion from pneumatically applied brake to hydraulically applied brake
Solution:
After evaluating the available technical information for the existing uncoiler, including its pneumatically applied tensioning brakes, as well as discussing project goals, constraints, and other technical requirements with the customer, Hindon determined that the upgraded retrofit braking system would need to be hydraulically applied, as a pneumatically applied system would not be capable of achieving the new torque requirement while still working within other application constraints.
Hindon therefore designed and supplied a braking system consisting of multiple hydraulically applied spring released disc brake calipers for use on a 35” brake disc with bolted hub and a new compact hydraulic power unit (HPU) for controlling the brakes. The calipers were positioned opposite of one another on the disc at approximately 180 degrees in the 9 o’clock and 3 o’clock positions. Exceeding the torque requirements of the previous brakes, the modern hydraulically applied spring-released brakes could generate maximum ~28,000 Nm of braking torque.
Upgrading the braking system on an aluminum mill uncoiler was necessary to enhance system reliability and accommodate increased production levels. The modern disc brake system designed by Hindon was an economical solution that provided increased torque, improved reliability, and could be manufactured and delivered within the end user’s project schedule and budget.