Background:
A leading manufacturer of brake shoes and disc brake linings for freight, locomotive, and transit vehicles approached Hindon in search of a solution for a bulk material handling issue affecting their manufacturing process. The customer required a solution that would enable them to efficiently discharge diverse material mixes from a dumper-fed bin to a weight scale. The process required accurate discharge of various materials stored in the silo into trays for molding brake shoes.
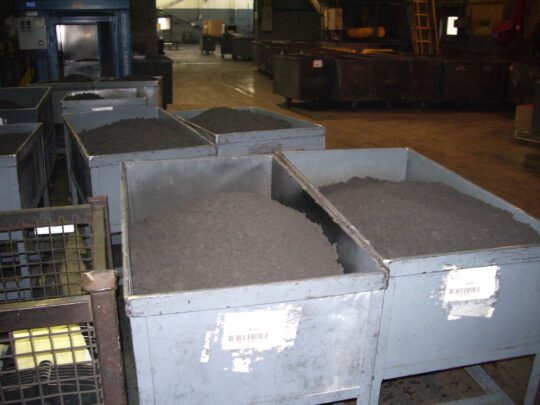
Materials used in the customer’s brake pad manufacturing process would be need to be stored in a silo and accurately discharged to reliably feed the downstream process.
The customer’s manufacturing process involved storing six different materials, each with its own unique material characteristics and flow properties, in a bin hopper for eventual metered discharge to the downstream manufacturing process. The varying bulk material densities, for example – which ranged from 25 lbs./ft.³ to 45 lbs./ft.³ – presented a challenge for storing and accurately discharging each of these different materials from a single silo.
The customer’s existing process used screw feeders and rotary valves to discharge material from the silo, but this equipment was not able to effectively handle materials with different densities, compressibility, and cohesiveness. The inability of the existing equipment to effectively handle the material presented the customer challenges such as sporadic feed rates, material sticking to bin side walls, and the screw feeders locking up entirely.
Given Hindon’s previous expertise using their ROPLEX rotary discharger™ to provide application-specific solutions to other difficult bulk material handling challenges, Hindon was a natural fit to support the customer with this application.
Application Challenges:
- Requirement to reliably discharge multiple materials with different bulk material handling characteristics from a single silo
- Difficult flowing materials with bulk material density ranging from 25 lbs./ft.³ to 45 lbs./ft.³
Solution:
To gain a deeper technical understanding of the challenging material mix, Hindon reviewed the customer’s bulk material test report to understand the different materials’ physical properties including particle size, density, moisture content, and cohesive strength. These physical properties determine the flow characteristics and behavior of the material under varying storage conditions. Hindon engineers used this information to inform their solution design including specifications such as proper silo wall angles, materials of construction, and discharge diameter.
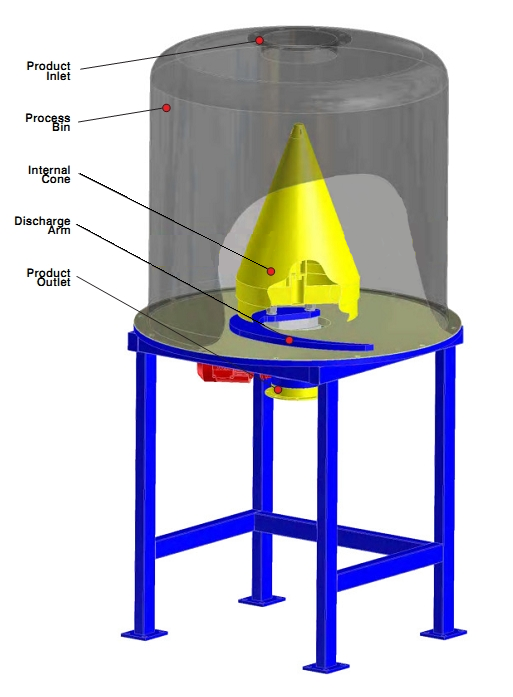
Illustrative model of the Micro-Feeder ROPLEX™ showing the basic design components
Hindon then designed, engineered, and manufactured a solution that involved retrofitting the existing silos with two 4’ ROPLEX™ rotary dischargers.
In principle, the ROPLEX discharger™ is a motorized rotary plow extractor providing a wide live opening for feeding the stored material. For ease of installation, adjustment, and maintenance, the ROPLEX™ was designed to adapt to the silo footprint and mounted externally to integrate with the customer’s existing dumper fed system. The stationary reclaim table mounted on the bottom of the silo was equipped with a special stainless-steel wear liner, making the unit suitable for dump-loading as well as handling the hot, corrosive materials used in the customer’s process and contributing to the overall maintenance-friendly design. An external motor drives a rotating pressure relief cone and curved plow that reaches to the edge of the reclaim table and undercuts the material head load, pulling the material into the central discharge opening effectively preventing the material from gaining a foothold on either the arm or the cone surface. This method of positive displacement ensures the uniform and complete draw down of material to achieve mass flow of the material from the silo.
By ensuring mass flow and eliminating the potential for rat-holing, the discharge rate could be easily adjusted from a minimum 43 lbs./min. to a maximum 124 lbs./min. The exact rate of discharge is easily controlled by the adjustable throat ring and VFD – this solution allows the customer to store and accurately discharge any of the material mixtures from the silo reliably and without flow stoppages.
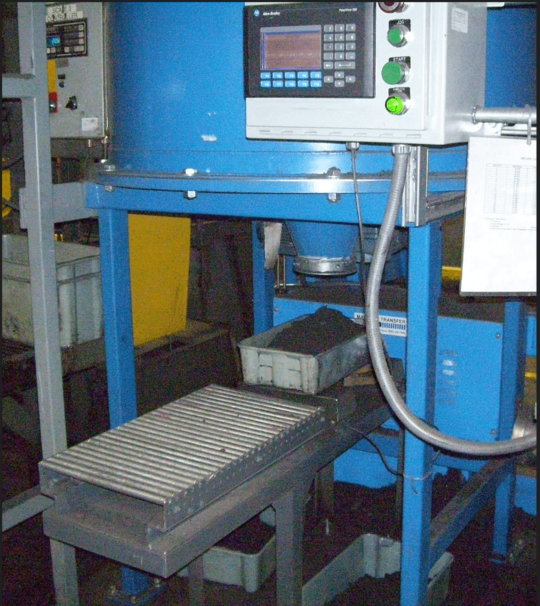
ROPLEX Discharger™ mounted to the bin for dispensing of the brake materials
After successful installation and commissioning of the first two ROPLEX™ units, Hindon later provided a third ROPLEX™ discharger to support the customer’s expansion of their manufacturing process.