Background:
A leading provider of material handling solutions approached Hindon to address the need for a dependable method of securing the horizontal rotary axis welding fixture used in their manufacturing process. Measuring 30’ long and weighing over 10,000 lbs., the large rollover positioner presented a considerable overhung load during operation, resulting in a significant safety concern. The customer required a robust solution to ensure the secure immobilization of their welding fixture.
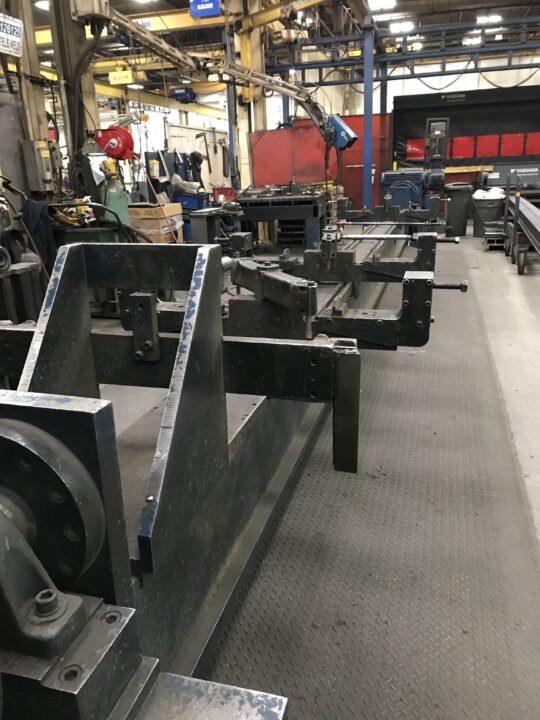
The customer’s welding fixture rotator measured 30′ long by 5 in height and width and presented a substantial overhung load during operation.
At the time, the customer’s weld fixture utilized a fail-safe drum brake which exhibited unreliable performance. After a preliminary review of the application and its technical requirements, Hindon determined that the existing brake was undersized. Given that the current brake lacked the required torque to safely secure the rotator in the event of a drivetrain failure, the customer needed a retrofit solution that would meet or exceed the specified torque requirements. Additionally, the ideal industrial braking system would seamlessly integrate with existing application constraints, providing a robust, readily installable, and cost-effective solution.
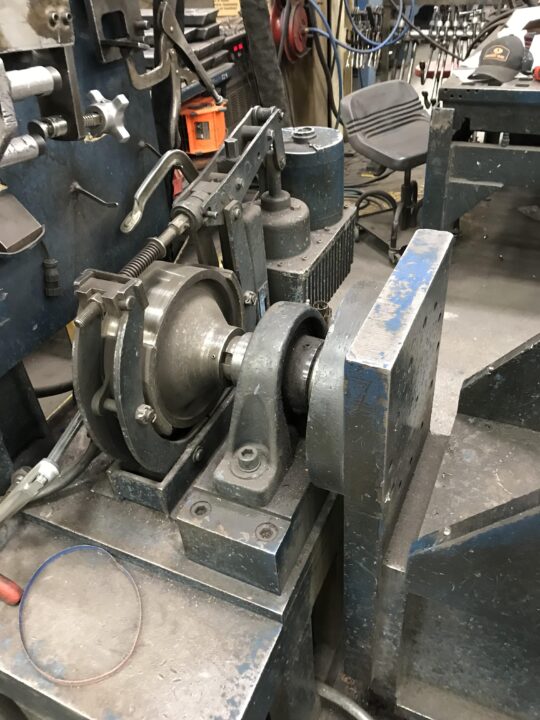
The existing drum brake on the welding fixture rotator was undersized for the torque requirement.
Solution:
Recognizing the deficiency of the existing brake, Hindon supported the customer in establishing the torque requirement for the new brake system. This was achieved through a comprehensive analysis of the weld fixture drivetrain’s technical specifications and the worst-case load torque due to horizontal axis rotation.
Hindon initially established the system’s center of gravity and mass under both loaded and unloaded conditions while rotating. This analysis yielded the nominal torque requirement, to which an appropriate safety factor was applied to determine the torque requirement of the upgraded braking system.
It was clear that a significantly larger and more robust braking system was necessary; a simple upgrade of the existing drum brake was insufficient to meet the new torque requirement. Because there was an existing shop air supply near the weld fixture, Hindon determined that a pneumatic disc braking system would be the most cost-effective solution for the project.
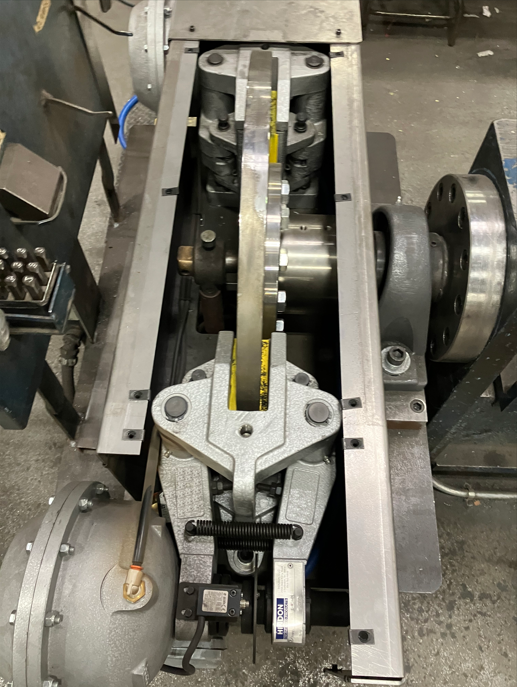
Overhead view of the retrofitted weld fixture brake following installation.
Hindon subsequently supplied an industrial braking system consisting of two spring applied, pneumatically released disc brakes for use on a 630mm diameter brake disc with bolted hub. The installation of this retrofit braking system was designed for simplicity and minimal modification to the weld fixture and shop environment.
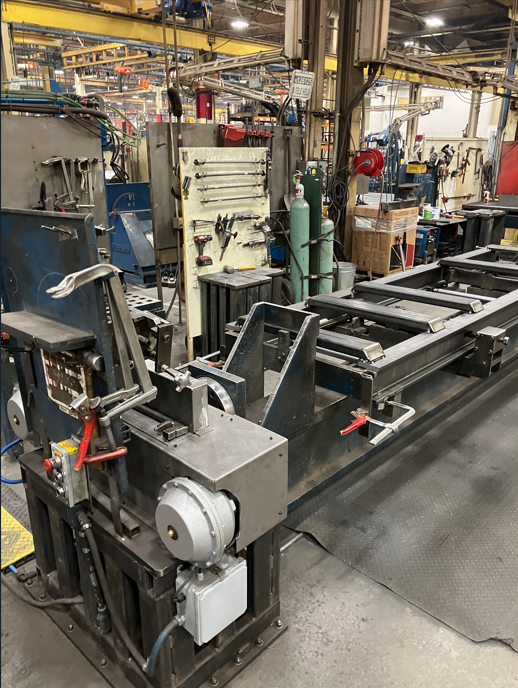
New weld fixture brake installed opposite the motor.
In the event of a failure, this new dual-caliper braking system from Hindon enhances safety by reliably immobilizing the rotary axis weld fixture.