Background:
A company specializing in engineering and fabricating custom industrial equipment in the Pacific Northwest was designing a steel uncoiler for a rolling mill and needed an industrial braking system to aid in handling 6,000 lb. coils. The equipment manufacturer came to Hindon in search of a braking solution to tension the material, stop the coil when the mill halted, function as a secondary holding brake when the mill was not in use, and allow for low-resistance manual unwinding. If necessary, the customer was open to using separate brakes to achieve these different functions, and they were also interested in examining the suitability of both pneumatic and electric solutions.
The customer was able to provide information about rotational speed and space constraints as well as the shaft diameter, but was initially unsure about the braking torque the uncoiler would need to be capable of to provide their desired tension on the coil.
Application Challenges:
- Integration of a braking system capable of tensioning, stopping, holding, and manual unwinding
- 11″ width space limitation
- Determining the required torque and brake disc size based on limited information regarding required tensioning force
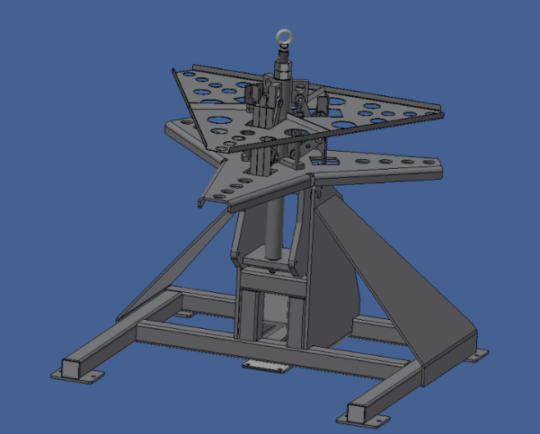
Steel uncoilers are commonly used to unwind and feed steel coils into a rolling mill, requiring steady tension to precisely control unwinding and prevent damage to both the coil and downstream equipment. The customer’s uncoiler had a clearance of only 11″ around its shaft, resulting in limited space for the new brake to be mounted.
Solution:
Weighing these constraints, Hindon provided a pneumatically applied disc braking system precisely engineered to provide exceptional performance and cost-effectiveness. A pneumatic disc brake is frequently the ideal choice for tensioning applications, demonstrating outstanding heat dissipation and torque adjustability via changes in air pressure. Although the steel coils weigh 6000 lbs., the uncoiler’s low rpm meant that a pneumatic brake would be able to safely and seamlessly function as not only a tensioning brake, but also a service brake and a holding brake for this application.
In addition to providing a simple system with minimal maintenance requirements, Hindon supported the customer with issues related to the implementation of the braking system, even when these items fell outside of Hindon’s scope. For instance, the customer was concerned about their existing lubricated pneumatic supply lines, but Hindon advised that the small amount of oil typically present in filtered, lubricated air would not compromise performance, with issues only arising with a significant oil presence.
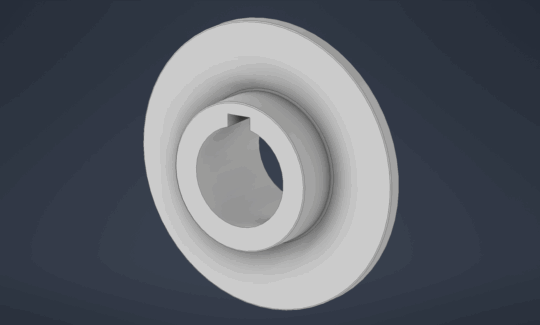
Hindon engineered and supplied this brake disc with an integral hub to maximize the disc’s annulus by eliminating the need for a bolted flange, thereby leaving more available space for the braking surface
Along with the pneumatic disc brake caliper, Hindon provided the complete hub and brake disc assembly. The solution included right hand and left hand pneumatically applied calipers, each used with a 250mm diameter x 12.7mm thick brake disc with integral hub. The special brake disc with integral hub design eliminated the need for a bolted flange, maximizing the brake disc’s annulus and ultimately allowing for the most compact braking solution possible. The brake discs were provided finished bored and keyed for easy installation onto the machine’s driveshaft.